Angstrom Sputter System
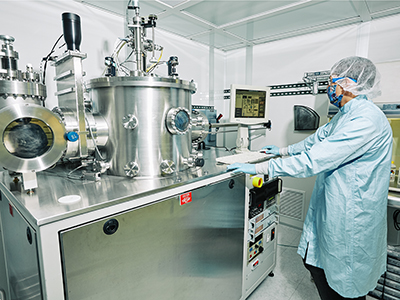
Description
The Angstrom Sputter System is a load locked sputtering deposition system for R&D applications. It can be used to deposit thin metal or dielectric films from three MAK 3” sputter targets powered by two 1000W RF and one 1000W DC power supplies. The MAK guns are also capable of sputtering magnetic materials.
Process gases: |
Ar, N2, O2
|
|||
---|---|---|---|---|
Sputter targets and processes: |
Aluminum,Carbon,Chromium,Cobalt,Copper,Gold*,Iron
Nickel,Nickel Oxide (reactive),Permalloy (80%/20%),Silicon (undoped or doped),Silicon Nitride (reactive),Silicon Dioxide, Titanium,Zirconium |
|||
*Additional usage fees exist for precious metal targets. At this time other targets available from MMF users are Indium Tin Oxide and Nickel. |
Operating Manual
*Note that the instructions below may not contain the most recent updates. Please refer to the manuals printed and posted at the equipment.
Thisphysical vapor depositionsputter tool isa researchgrade instrument withthree targets,two RF power supplies, one DC power supply, substrate heating, and multiple process gases.
- This tool contains high voltage sources. Do not go behind the tool, attempt to open covers, or work inside the tool.
- Avoid pinching your fingersin theload lockdoor.
- Use caution to avoid bumping your head when the door is openor on the transfer arm.
- After long depositions, the sample stage may be very hot. Use caution.
- If the tool is on fire orif someone is in immediate danger, hit theemergency stopon the front of the tool.
- Target link: (inprogress)
- Do not attempt to make your own recipes without extensive training and permission from the lab manager.
Aluminum thin film
- Thin films of aluminum can be deposited via sputtering or evaporation.
Chrome thin film
-
Chrome RF sputter deposition.
dep rate= 9.4nm/min, power=400W RF, pressure=10mT Argon, substrate height =120
Gold thin film
- Thin films of gold can be deposited via sputtering or evaporation. Ebeam and resistive thermal evaporation are available.
Iron thin film
- Thin films of iron can be deposited via sputtering.
Permalloy thin film
- Thin films of permalloy can be deposited via sputtering.
Silicon Dioxide thin film
- Thin films of silicon dioxide can be deposited via sputtering.
Titanium thin film
- Thin films of titanium can be deposited via sputtering.
- Check tool status and configuration
- Visit this link to reserve the tool.
- Request different targets, shields, or gases as far in advance as possible, preferably at least two weeks, by emailing the lab manager and mmfstaff@montana.edu.
- Check tool reservations for conflicts and reserve the tool
- Check lab status
- Turn on N2 for the lab and check the house N2 bottle pressure. If it is below 300 PSI, report the shortage to staff.
- Check process gas bottle pressures (Ar, O2, N2). If any are below 300 PSI, report the shortage to staff.
- Check that the correct process gas is selected for your process. O2 and N2 can be switched; request a change with staff if necessary. Do not attempt this process without explicit training from the staff and accompanying documentation. It is very easy to contaminate the gas lines.
- Log into SUMS.
- Log into the Angstrom software using “Supervisor” and “Supervisor” for the username and password. Log into the Sigma software with the default username and leave the password blank.
- Equipment checks
- Check deposition chamber pressure. The ion gauge should read <5e-7 Torr if left overnight or <1e-6 Torr if recently used. The convectron and baratron gauges should read “Off Scale”.
- Check that the cryo temperature is below 14 K. If the temperature is <18 K, use the tool but report the problem to the lab manager. If the temperature is >18 K, do not use the tool.
- Check that the load lock is under vacuum. It should be <10 Torr. Note that there is no ion gauge connected to the load lock, so this reading is meaningless and can be ignored.
- Double check the target configuration by selecting “BASE FLANGE DETAIL”.
- Check mass flow control settings
- Check which gases are currently connected to the tool. Ar is always connected, but N2 or O2 can be selected. Check the valve on the wall behind the tool under the pressure gauges on the inside of the wall.
- Check the MKS 4 Channel Readout. Any channel set to “Rem” will turn on during a process. Ar is connected to channel 1, and either N2 or O2 is connected to channel 3. For most processes, only Ar is used, so the other channels should all be in the “Off” position.
- Check pressure control settings
- The VAT Adaptive Pressure Controller should have the “Remote” and “Open” LEDs on. If “Local” is lit, press and hold “Remote” until that LED turns on. You may need to reset a fault on the Angstrom software.
- Check power supplies
- Check that the required power supplies are on. The RF supplies should be on and should read “Remote OFF” in the upper right corner. They should also read “auto” under the diagram of the matching capacitors.
- Verify “VAT GATE VALVE” is open.
- Load samples
- Vent load lock
- Unscrew and unlatch blue knob on load lock.
- Select “AUTO”, then “LOAD LOCK AUTO VENT MODE SELECTED”
- Click “SELECT” on verification
- Click “START SELECTED CYCLE”
- Load samples on sample holder. Note that most of the thickness variability will be radial because of sample rotation, so expect thickness variations from the center to the edge of the sample holder. Verify that all screw holes are covered and that all screws are fully tightened down. You are welcome to use screws or Kapton tape to secure your samples.
- Load sample stage in load lock
- Set stage in the bayonet mount.
- Orient screw toward you.
- Raise sample stage all the way up if you plan to do load lock sputtering.
- Pump load lock
- Vent load lock
-
-
- Close the door and gently tighten the handle.
- Select “AUTO” and then “LOAD LOCK FULL PUMP DOWN MODE SELECTED”
- Click “START SELECTED CYCLE”
- Expect to hear the pump turn on.
- Wait for load lock convectron gauge to read “Off Scale”. This happens a few minutes after the automatic process is complete.
-
- Clean sample in load lock (optional)
- Ensure the sample stage is all the way up.
- Enter manual mode by selecting “MANUAL”.
- Close the “LL HIGH VAC VALVE” and open the “LL GATE VALVE”.
- Run MMF-LoadLock or other cleaning process from the Sigma SQS-242 software.
- Double check the recipe is correct.
- Transfer sample
- Ensure load lock convectron gauge reads “Off Scale”.
- Open “LL GATE VALVE”.
- Turn on lamp.
- Make sure ruler on top of chamber (stage height ruler) is set to a height above 85 mm (i.e. smaller number than 85 mm).
- Carefully and smoothly move the transfer arm all the way into the load lock.
- Lower the sample stage onto the transfer arm fork. Do this slowly and carefully, while making small adjustments to the rotation and transfer arm position. If the fork starts to bend downward, stop and assess. Make sure the stage sits flat on the fork. When the sample stage is resting on the fork, raise the bayonet mount so that the sample stage can be moved into the main chamber.
- Carefully and smoothly move the transfer arm to the main chamber transfer position.
- Use the motorized stage to lower the main chamber bayonet mount and lift the sample stage.
- Fully retract the load arm.
- In manual mode, close the “LL HIGH VAC VALVE” and “LL GATE VALVE”.
- Lower or raise the sample stage to the desired height for deposition (120 mm for standard recipes).
- Deposit
- Open the appropriate database and select the desired process. Do not edit anything but the process time in the MMF-Standard-Recipes database.
- Edit the process if necessary.
- Click “START PROCESS”
- Monitor the tool during ramp up and during the deposition.
- Verify that the plasma strikes. If it does not by the time the supply reaches about 100 W, stop the process. See the troubleshooting section.
- After the plasma strikes, close the view port shutter slowly. If this shutter is opened or closed quickly, it can get stuck. Open it periodically to view that the process is proceeding as expected.
- Verify that the source shutter opens when process starts and that the stage is rotating.
- Verify that the reflected power decreases to <5 W and remains at that level during the deposition.
- Verify that the sample shutter opens after the ramp and hold steps.
- Unload sample
- After the deposition, wait for the sample temperature to read <70 C on the “SAMPLE HEATING” reading next to the EMO. Below the angstrom engineering sign.
- Raise the sample holder back to < 85 mm.
- Open the LL Gate Valve
- Move the transfer arm back to the main chamber’s loading position.
- Set sample holder onto transfer arm’s fork using the z-height controller and rotation knob.
- Once the sample holder is loaded onto the transfer arm’s fork, open the load lock gate valve and move the sample holder to the load lock’s unloading position.
- Unload the sample holder and fully retract the transfer arm.
- Close load lock gate valve.
- Select “load-lock auto vent” and wait for the cycle to complete.
- Once the load lock is completely vented, open the load lock’s door and remove the sample holder.
- If finished depositing, return the sample holder to the LL, close the load lock’s door and tighten the blue knob. Select full pump down and let cycle complete.